A Bill of Materials is a list of constituent items along with quantity details that can be allotted for the manufacture of a certain product, by-product or likewise. This facilitates immediate reduction in stock of the item automatically. This process of listing the items that make up another item is made possible in Tally by enabling the Bill of Materials Facility.
Bill of Material (BoM) is created only for those items that are being assembled in-house. Therefore, you need to specify a BoM at the time of creating a Stock Item or while altering the stock item. For trading items, you do not need a BoM.
Bill of Material feature is useful for manufacturing organisations and can be set up through F12: Configure
1. Setup Bill of Materials (BOM)
Gateway of Tally > Create > type or select Stock Item > and press Enter.
Alternatively, press Alt+G (Go To) > Create Master > type or select Stock Item > and press Enter.
Press F12 (Configure) > set Set Component List (Bill of Materials) in Stock Items to Yes to allocate Bill of Materials for the stock item.
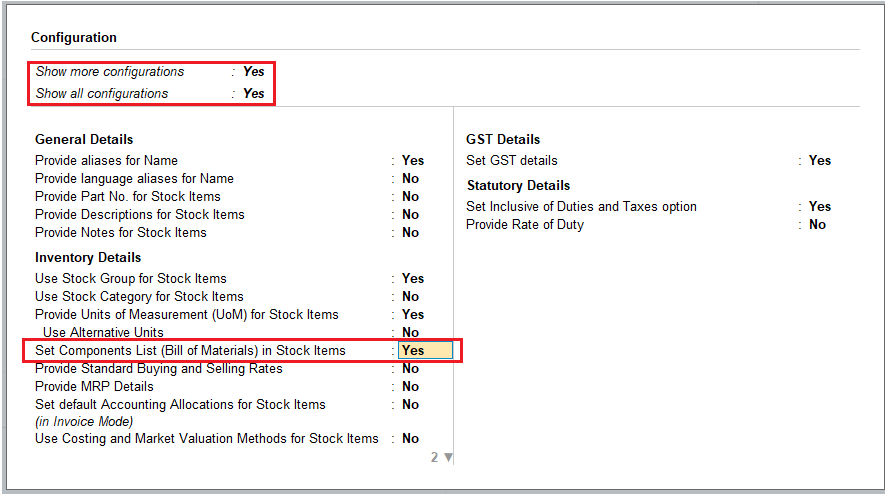
340
If you do not see this option, set Show more configurations to Yes.
If you need to use this option only for the current master, press Ctrl+I (More Details) > type or select Component list (BoM) > and press Enter.
In the Stock Item Multi Components (M BOM) screen specify the required details.
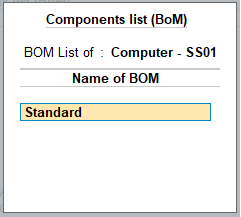
341
Example:
Swayam Sales decides to Assembles a Computer of his own Brand i.e. Computer – SS01 ( GST-18%) to be Sold in the market with the following 11 Components..
Name of Components | Qty. | Price |
Cabinet | 1 Nos. | 4500 |
CD Drive | 1 Nos. | 600 |
Keyboard-Logotech | 1 Nos. | 1500 |
Motherboard Intel | 1 Nos. | 12600 |
Mouse – Logitech | 1 Nos. | 500 |
Processor – Intel | 1 Nos. | 4500 |
RAM 8 GB | 1 Nos. | 3200 |
HDD Seagate 2 TB External | 1 Nos. | 6000 |
Monitor SONY 20” | 1 Nos. | 16000 |
UPS Apc | 1 Nos. | 1600 |
Windows XP | 1 Nos. | 4500 |
Total Components Costing | 55,500 | |
Add: Installation Charges | 1,500 | |
TOTAL COSTING | 57,000 |
Solutions:
Create the item ‘Computer-SS01’ with Units – Nos. and Set Components (BOM) – Yes with above components as screen shown :
1. Gateway of Tally > Create > type or select Stock Item > and press Enter.
Alternatively, press Alt+G (Go To) > Create Master > type or select Stock Item > and press Enter.
2. In Stock Item Creation screen
- Enter the Stock Item Name , select the appropriate Stock Group and specify the appropriate Unit of Measurement in Unit field
- Set Component List : To create the component list required to manufacture the Finished goods enable this option to Yes
3. Press Enter to view Stock Item Multi Components (M BOM) screen
4. In Stock Item Multi Components (M BOM) screen
- Under Name of BOM specify component list Name – Standard and press enter to view Stock Item Components (BOM) screen
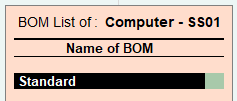
342
5. In Stock Item Components (BOM) screen:
- BOM Name : By default the BOM Name specified in Stock Item Multi Components (M BOM) screen will be defaulted and application will not allow to move the cursor to BOM Name field.
- Components of : In this field application displays the Name of the Stock Item for which the components are defined.
- Unit of manufacture : Specify the appropriate number of finished product that will be manufactured by using the components identified in the component list.
- Item : In this field identify the raw materials which are required to manufacture the finished goods
- Godown : If there are multiple Godowns or Locations, specify the storage location of the items from where the items will be used for manufacture.
Note: The godown option will be displayed only when Maintain multiple Godown feature is enabled in F11: Features (Inventory Features)
- Quantity : In this field mention the quantity of Raw Material required to manufacture the finished goods.
Observe to create the product Computer-SS01we require 11 different products . The Quantity of Products required to assembled Computer-SS01 is 1 each of 11 different products.
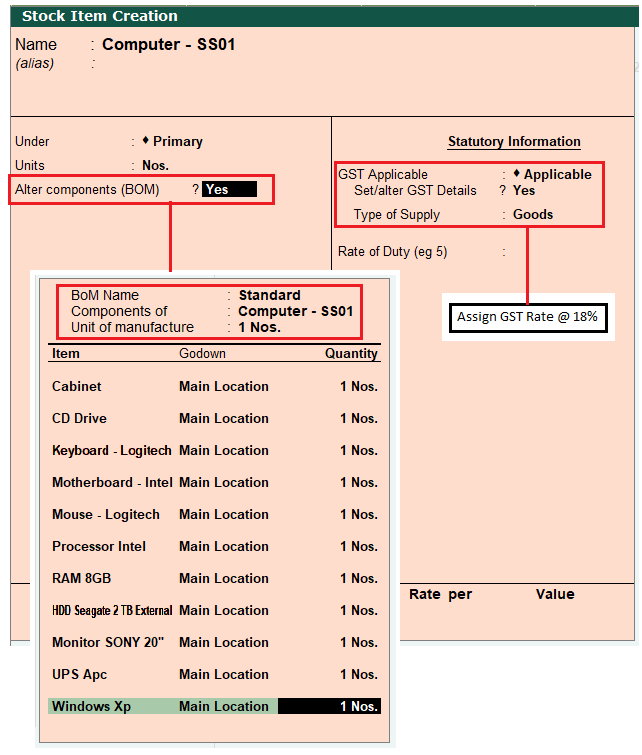
343
- Specify other required details in the stock item master and accept the screen.
2. Creating a Manufacturing Journal
Creating Manufacturing Journal for a Stock Item with Single Bill of Materials . All the manufacturing transactions can be accounted through a Stock Journal (F7: Stk. Jrnl).
To record manufacture of finished goods in Stock Journal – Alter the Voucher Type by setting the option Use as a Manufacturing Journal to Yes . Or
Create a Manufacturing Journal under Stock Journal by setting the option Use as a Manufacturing Journal to Yes.
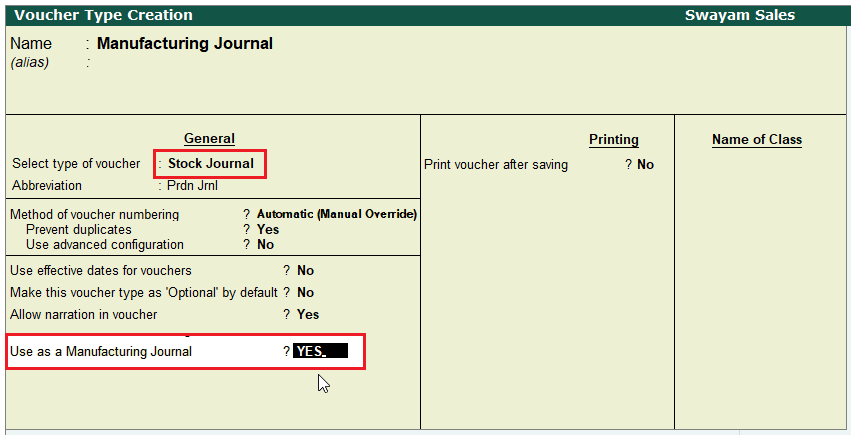
344
Note: Bill of Material should be created before accounting the manufacture of an item.
1. Go to Gateway of Tally > Vouchers > press Alt + F7 (Stock Journal)
Alternatively, Press Alt+G (Go To) > Create Voucher > press Alt+F7 (Manufacturing Journal).
If you have created a new voucher type Manufacturing Journal , a pop-up menu will be displayed with the options default Stock Journal and Manufacturing Journal.
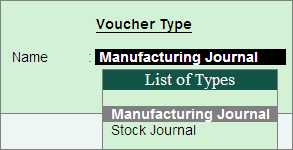
345
Select Manufacturing Journal to view the Manufacturing Journal voucher creation screen
- Name of Product : Select the product which needs to be manufactured from the List of Items.
- BoM Name : In this field the BoM created for the stock item will be displayed automatically with one more option Not Applicable .
Note: The list of Raw materials required for the manufacture of finished goods will be displayed in Components (Consumption) side based on the BOM defaulted.
- Quantity : In this field specify the quantity of finished goods manufactured.
- Components (Consumption) : In this section the components required to manufacture the finished goods will be displayed automatically based on the components defined in the BoM.
Quantity of Raw material will be defaulted based on the quantity requirement defined in the BOM multiplied by the Quantity of finished goods manufactured.
- Installation and Service Charges extra of Rs.1500 to assembled a Computer . So the Costing to assembled a Computer-SS is Rs. 57,000
The completed Manufacturing Journal is displayed as shown
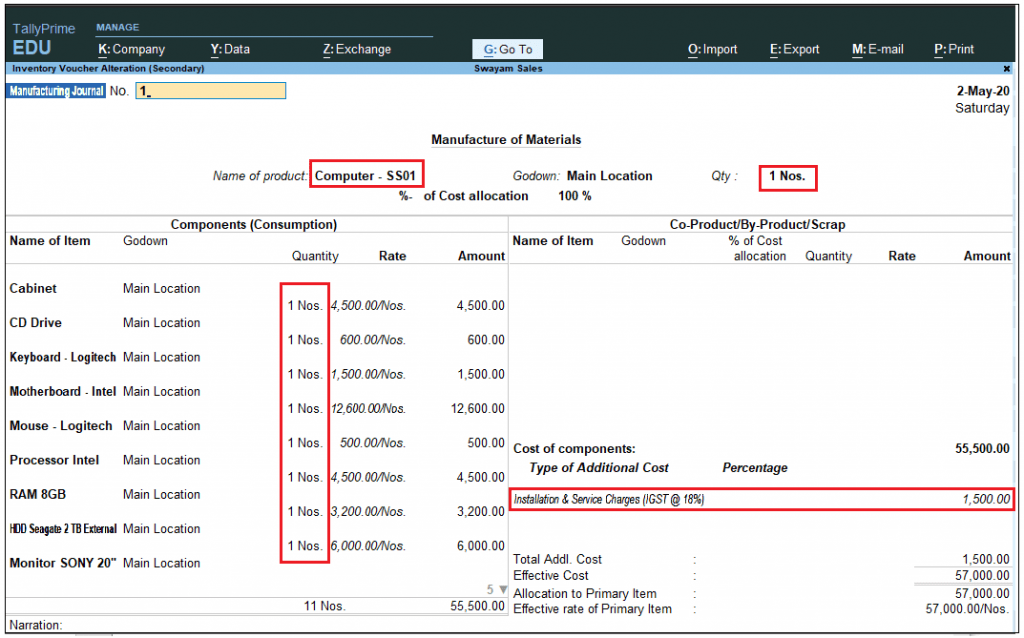
346
Accept the screen. As always, you can press Ctrl+A to save.